1. Types of pressure sensors
In industrial practice, pressure sensors are one of the most commonly used types of sensors. They are widely employed across various industrial automation environments, including sectors such as aerospace, military, petrochemical, power, and many others.
Depending on the type of pressure being tested, these sensors can be classified into gauge pressure sensors, differential pressure sensors, and absolute pressure sensors.
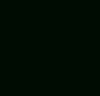
Gauge pressure sensors are capable of sensing pressures relative to atmospheric pressure.
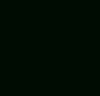
Differential pressure sensors can measure the difference between two pressures.
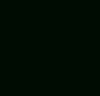
Absolute pressure sensors measure absolute pressure. Here, absolute pressure refers to the actual pressure exerted on an object, calculated from the standpoint of a vacuum state.
2. The new pressure sensor
Conventional pressure sensors are mechanical and have substantial size and weight, no electrical output, and lower levels of precision. They are also not conducive to information transfer.
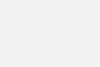
With the advancement of technology, a new generation of pressure sensors was developed. They are smaller, lighter and are extensively used in various fields.

They can convert changes in pressure into alterations in resistance. However, resistance changes are not easily collected directly as signals. Therefore, we also need to convert changes in resistance into changes in voltage or current to facilitate the capture of data by data acquisition device.
To accomplish this conversion, we would require a special circuit known as the Wheatstone Bridge. This circuit can accurately measure changes in resistance. However, this voltage value is relatively small, usually in millivolts.
On the sensor, it is denominated as mV/V, representing the sensor’s sensitivity. If the sensor has a sensitivity of 2mV/V and the excitation voltage is 10V, the full scale output of the sensor will be 20mV. To use this small output voltage, it needs to be amplified to a standard voltage by an amplifier or operational amplifier.
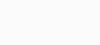
3. The acquisition device collects the pressure sensor signal
In the upcoming experiment, we will use the SRD-1004 programmable amplifier to amplify the data collected from the pressure sensor and transmit this data to the USB-3123 data acquisition device.
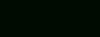
The SRD-1004 programmable amplifier can be used either by software or a dip switch, to control the magnification, and it can also provide a 5V DC power supply for the sensor.

To set up the amplifier accordingly.
First, flit the Switch EN to enable control of the amplifier by the DIP switch for magnification adjustment. Then, flip switches No.1 and No. 2 at PGA 0 to set the PGA 0 amplification multiple to 1,000 times. The pressure sensor we are using has a sensitivity of 2.0mV/V and a range of 5 kg.
In this experiment, we are providing a voltage of 5V to the sensor, so the full-load output is 10mV. Amplifying the sensor output voltage 1,000 times means the maximum output voltage would be 10V, which complies with the range of the acquisition device. This shows that the amplification multiplication of the amplifier is appropriate.
Now let’s look at the connection schematic to see how to connect all these components together.
First, connect the power line of the sensor with the power supply of the amplifier. Then, connect the positive and negative signal lines of the sensor to the positive and negative signal input ends of the amplifier. Once done, connect the output signal end of the amplifier to the AI0 end of the acquisition device, and at the same time join the GND end of the amplifier to the AI Sense end of the acquisition device. Also remember to short the AI Sense end of the acquisition device with the AGND end. Finally, use a USB cable to connect the amplifier and the acquisition device to the computer.
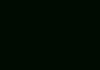
Open the corresponding software and adjust the parameters of the acquisition device. Set the sampling rate to 5kSa/s/ch.
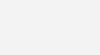
Then turn on the unit conversion and set the sensor range. The upper limit is 5,000 and lower limit is -5,000, the output voltage lower limit is -10V and upper limit is 10V, and the unit is in grams.
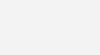
The reason for setting the positive and negative values is that the sensor represents tension as a positive value and pressure as negative. After making all of these settings, proceed to adjust the canvas. Lock coordinates from -5,000 to 5,000 and turn off the automatic Y-axis adjustment.
Once you start the test, we should be able to see that when the sensor is not under any force, the measurement is on the 0 scale line.
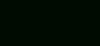
If you place a 500g weight on the sensor, you’ll see that the data acquisition device collects data showing -500.
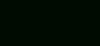
Applying tension to the sensor will result in a positive value.
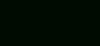
The above is our measurement of static pressure, but the most significant advantage of the data acquisition device lies in capturing transient pressure. Adjust the sampling rate of the acquisition device to 10,000, and it’ll respond well to instantaneous pressure. The rest of the settings remain unchanged.
Adjust the horizontal coordinate of the canvas to 0 to 30 to facilitate our observations. Once all adjustments are complete, strike the sensor with a screwdriver. You’ll see that the instantaneous pressure is captured on the canvas. Using the hand tool to adjust the horizontal coordinates, you’ll be able to clearly see the pressure changes when the sensor is struck.
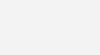